В деятельности любой компании (производство, транспорт, медицина, гостиничный бизнес и пр.) существуют скрытые потери. Эти потери увеличивают издержки производства, не добавляя потребительской ценности для заказчика. Они увеличивают срок окупаемости инвестиций и ведут к снижению мотивации сотрудников. На выявление и устранение этих потерь направлено использование инструментов бережливого производства.
Бережливое производство (lean production) – это система организации производственного процесса, позволяющая произвести больший объем продукции/услуг при меньших усилиях, на меньших производственных площадях и оборудовании при полном удовлетворении ожиданий потребителя. Бережливое производство составляет основу новой философии менеджмента.
Идеи бережливого производства впервые были сформулированы и внедрены ещё Генри Фордом. Но эти идеи носили характер разрозненных мероприятий и не затрагивали само мировоззрение работников. Было создано поточное, малозатратное производство, и автомобиль марки Форд-Т, не имел конкурентов в мире по цене, качеству, уровню удовлетворённости. Но идеи Форда не получили широкого распространения, так как экономика страны развивалась динамично, рынок был закрыт для других государств, существовали возможности для экстенсивного развития
Отцом-основателем бережливого производства считается Тайити Оно (1912-1990 гг), начавший работу в Toyota Motor Corporation в 1943 году, привнеся в компанию лучший мировой опыт. В середине 1950-х годов он разработал и внедрил систему Toyota Production System, TPS, которая в западной интерпретации стала известна как Lean Production, Lean Manufacturing, или просто Lean. Термин lean был предложен Джоном Крафчиком, одним из американских консультантов. В компании "Тойота" была создана система, цель которой - сократить или ликвидировать деятельность, потребляющую ресурсы и не добавляющую стоимость, т.е. ту, за которую потребитель не желает платить.
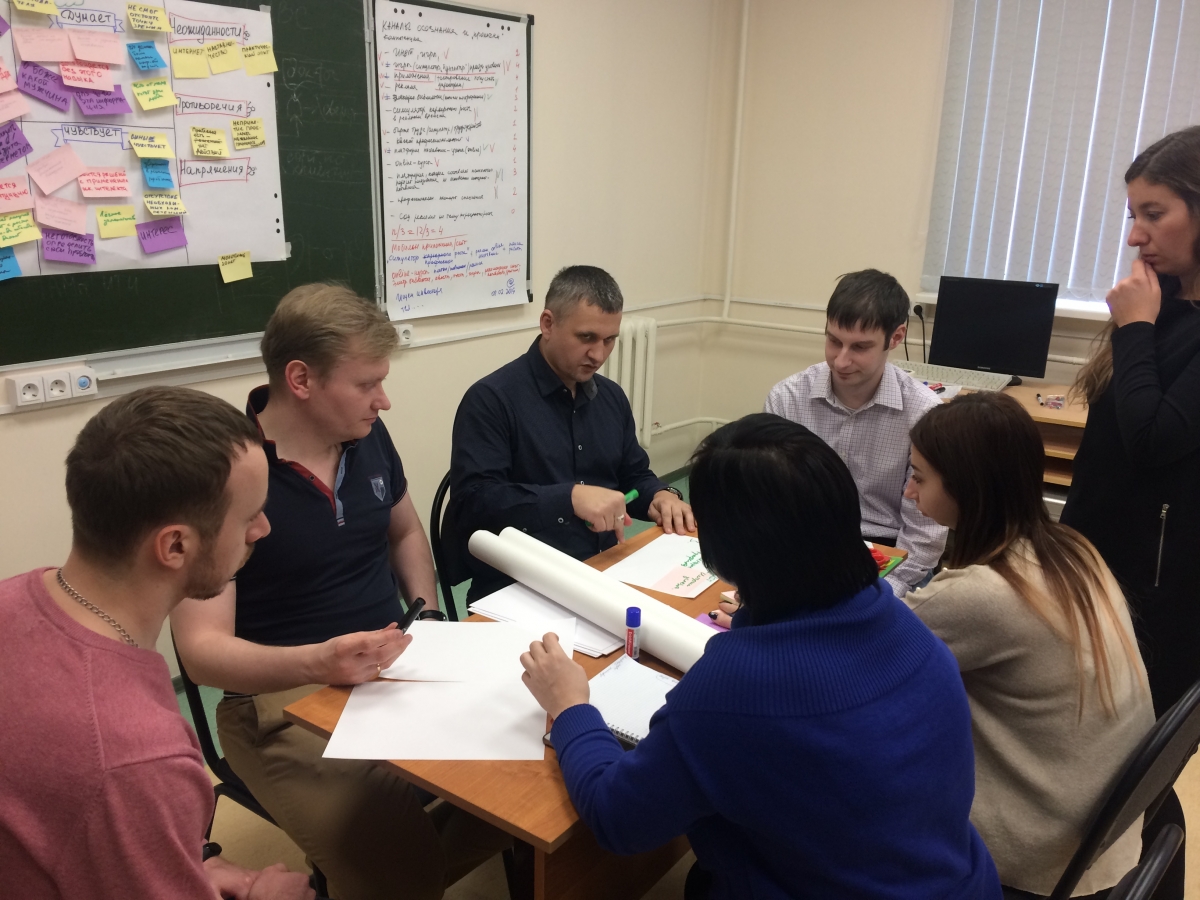
Многие из элементов были разработаны в СССР в такой области знаний как научная организация труда (НОТ).
Мировой опыт показывает следующие результаты внедрения компаниями инструментов бережливого производства:
- рост производительности труда
- сокращение времени производственного цикла
- сокращение брака и рост качества продукции
- сокращение времени простоев оборудования
- высвобождение производственных площадей
Лин Шесть Сигм (Lean Six Sigma) - комбинация двух наиболее популярных в мире подходов. В отличие от японской модели бережливого производства «Лин», «Шесть Сигм» родилась в США, это созданная Motorola и усовершенствованная General Electric методология оптимизации, опирающаяся на математические модели. Обе концепции нацелены на непрерывное совершенствование, и в результате методология Лин Шесть Сигм позволяет получить эффект как за счет снижения потерь, так и за счет построения стабильных и контролируемых процессов.
В рамках программы MBA «Управление производством», реализуемой Высшей школой менеджмента, с бережливым производством связан большой блок дисциплин («Производственные системы», «Управление эффективностью», «Бизнес-процессы», «Бережливое производство»). Эти дисциплины проводятся в формате лекций, мастер-классов, тренингов, выездных мероприятий по обмену опытом с передовыми компаниями.
Особенный интерес у слушателей вызывает применение такого подхода, как DMAIC (D – определение, M – измерение, A – анализ, I – совершенствование, C – контроль).
На этапе «Определение» основная задача команды – обозначить проблему и цель. Далее составляется карта SIPOC - это инструмент для визуализации процесса, для формирования единого понимания всеми членами команды основных шагов процесса. Это очень эффективный коммуникативный инструмент, который дает всем членам команды одинаковое представление о процессе, а также информирует руководство о том, над чем работает команда. Затем составляется перечень требований клиента. Это происходит посредством методики «Сбор голоса клиента». Голос клиента – это его наиболее характерные высказывания. Следующим шагом на данном этапе является разработка паспорта проекта. Завершается процесс определением необходимости изменений и идентификацией заинтересованных лиц.
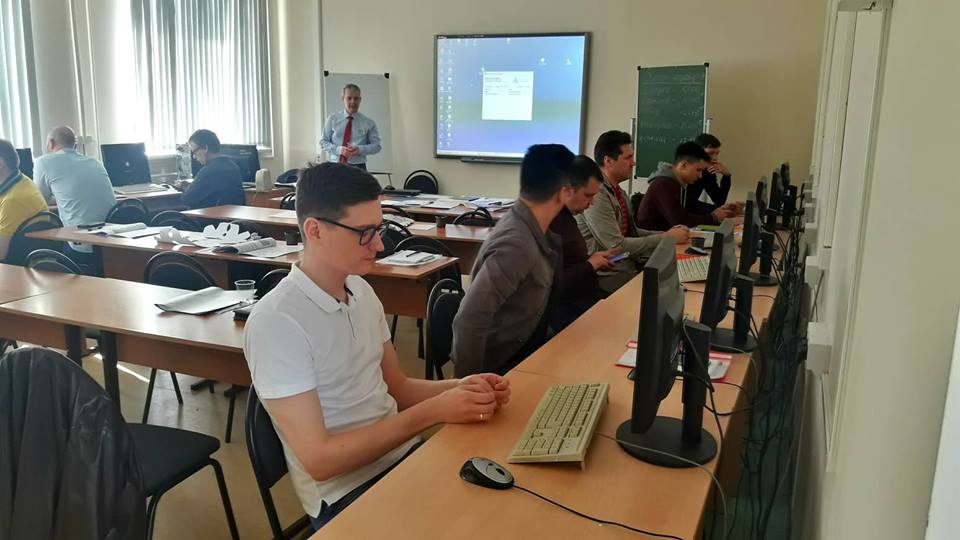
Этап «Измерение» включает в себя составление карт процесса (диаграмма Спагетти, MIFA, VSM). Карта потока создания ценностей (VSM) показывает взаимосвязь между деятельностью, задачами и людьми, выполняющими эти задачи; позволяет сократить сроки процесса. MIFA применяется, если проект нацелен на уменьшение ошибок или если в процессе много разных подразделений-участников. Диаграмма Ишикавы – визуальный инструмент, отражающий отношение между следствием (проблемой) и его возможными причинами. Важным моментом на данном этапе является составление плана сбора данных, который определяет, какие данные, в каком объеме, когда и как будут собраны. Завершающий шаг данного этапа – расчет Сигмы (определение бездефектности процесса).
На фазе «Анализ» производится анализ SWIIMTOO, который помогает определить 8 основных источников потерь. Немаловажным в процессе анализа является определение времени такта: расчет темпа (такта), с которым должен работать процесс, для выявления узких мест и последующей балансировки процесса. Время такта – это скорость, с которой процесс должен приносить результат, чтобы соответствовать запросам клиентов. Наряду с этим, используются такие методики, как диаграмма соответствия, древовидная диаграмма, «5 почему», диаграмма Парето, матрица приоритезации.
На фазе «Совершенствование» первым шагом осуществляется выработка потенциальных решений путем применения техник креативности (техники мозгового штурма), бенчмаркинга, краудсорсинга. Последующим шагов становится выбор решений (N/3, матрица выбора решений) и проверка решений (карта будущего состояния, пилот). Карта будущего состояния – это документ, отражающий все изменения, которые уже произошли или только планируются; пилот – это пробное внедрение в меньшем масштабе. Главный шаг на данном этапе – это разработка планов внедрения. Этот шаг подразделяется на следующие разделы: оценка последствий (FMEA – анализ характера и последствий отказов, защита от ошибок), планирование внедрения (план внедрения, план коммуникаций), оценка экономического эффекта, внедрение решения.
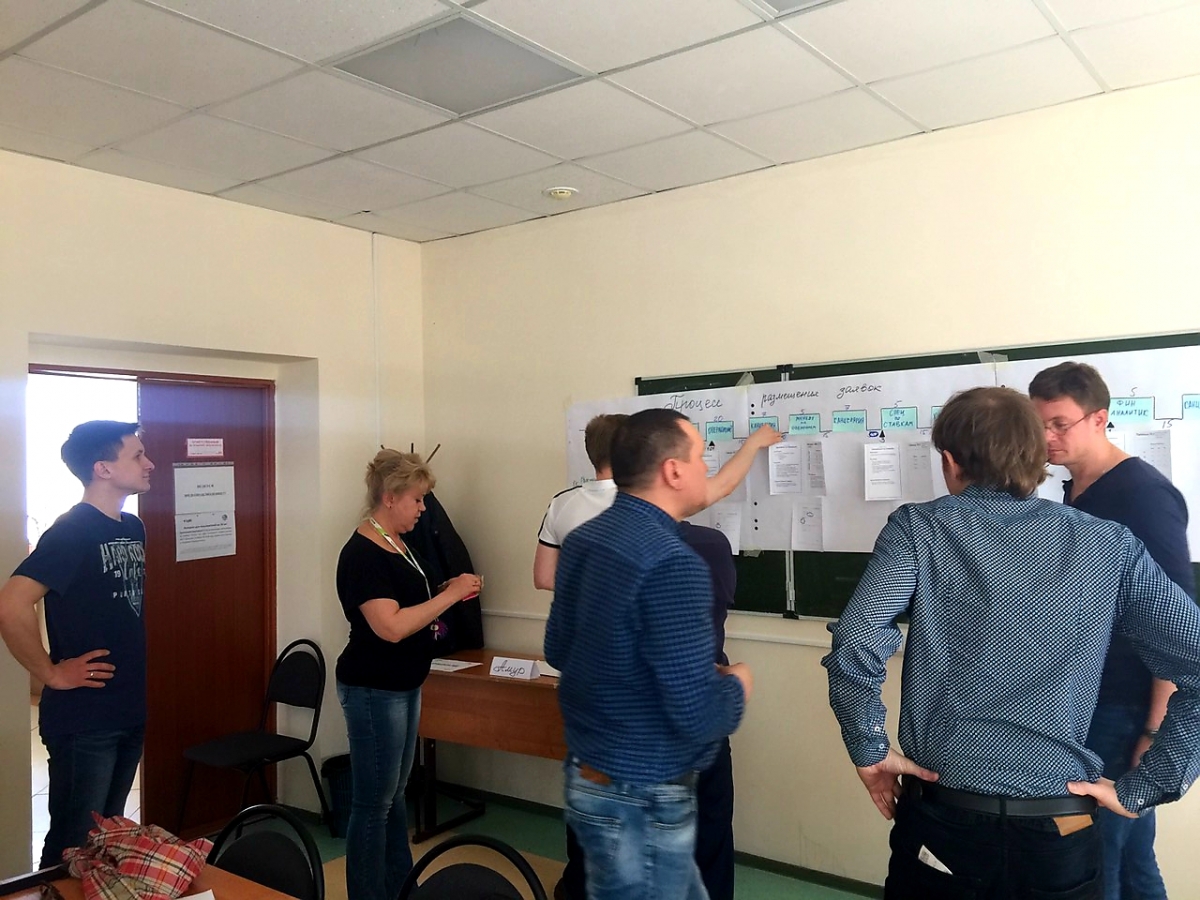
Фаза «Контроль» включает в себя такие процессы, как разработка системы контроля и закрытие проекта. Составляется План контроля процесса для мониторинга и поддержания достигнутых результатов. Это матрица, содержащая ключевую информацию по новому процессу, а также перечень постоянно контролируемых показателей и подходов по мониторингу и реагированию на отклонения. Для наглядности составляется панель управления – графическое отображение 6-8 основных показателей, указанных в Плане контроля процесса. Завершать этап рекомендуется составлением резюме – кратким описанием проекта на одной странице для коммуникационных целей.
Интеграции двух методологий, которые друг друга дополняют и дают больший синергетический эффект, активно применяется, например, в Сбербанке. Опыт Сбербанка и других международных компаний, которые также пользуются этим набором инструментов, подтверждает высокую эффективность методов лин-технологий.
Ведущими преподавателями по блоку дисциплин, связанных с бережливым производством, выступили руководитель Управления ПСС и процессов Поволжского банка Сбербанка С.Котельников и эксперты Управления Т.Новоженина, Р.Басыров, С.Гадельшина, И.Петрушин.